IMPERIAL STEERING GEAR INTERNAL CHANGES
- Ports in valve body .090" diameter (were .187") (Dampens road shock - reduces shimmy)
- Reaction pressure plates .008" thick (were .006") (Provides increased "road feel")
|
|
IMPERIAL CONVERTIBLE IDLER ARM DAMPER
- Bolted to bracket on frame side rail.
- Idler arm mounts on serrated shaft.
- Hydraulicly dampens rapid movement (shock or shimmy), but does not retard steering action.
- Rotates with same feel as shock absorber. Serviced by replacement only.
|
|
IMPERIAL FULL BALL TIE ROD ENDS
- Self adjusting, low friction, long life.
- 32,000 mile lubrication.
- Bleeding type seals.
|
|
IMPERIAL STEERING COLUMN WITH LOWER BEARING
- Lower bearing with insulator.
- Coupling with 7 ply flexible disc.
- Floor support,"O" ring and plate.
- Install upper bearing housing (general design and service procedures same as other Corporation cars).
|
|
IMPERIAL COLUMN - LOWER END
- Position lower seal on shaft (lubricate seal).
- Center lower bearing on shaft serrations (lower bearing .007" larger I.D. than upper, and has red separator. Upper bearing has white separator or no separator).
- Install insulator on lower bearing and install shaft assembly in column.
|
|
IMPERIAL COLUMN UPPER END
- Install snap ring, upper bearing and remaining parts (same procedure as 1963 V,L,P,D,C).
|
|
IMPERIAL GEAR AND COLUMN ALIGNMENT AND COLUMN INSTALLATION
- Gear must be realigned if mounting is disturbed.
- Loosely mount gear on side rail.
- With tool C-3949 bottomed on wormshaft support, and thumbscrew at 12 o�clock, tighten thumbscrew and install clamp at instrument panel with tab in slot.
- Tighten two front bolts, firmly position wedge by tapping lightly with hammer, then tighten rear bolt.
- Remove tool and install column assembly with:
- Master serrat ions aligned
- Locating pin in coupling bottomed against wormshaft (Install and tighten coupling bolt)
- Flexible coupling disc axially unstressed.
- Tab on instrument panel clamp engaged in slot.
- Do not let top of column fall or damage to coupling disc or horn wire will result.
|
|
- Tighten main support plate
- Slide "O" ring into place
- Tighten "0" ring retaining plate
|
|
STEERING COLUMN WITh TILT WHEEL
- Optional on Imperial, Chrysler and Dodge 880.
- Raise release lever to select one of seven positions.
|
|
REMOVAL AND INSTALLATION OF TURN SIGNAL SWITCH
- Bowden cable engages switch pin.
- Switch screws tightened with wheel tilted down.
|
|
REMOVE TURN SIGNAL COVER
- Remove tilt and turn signal levers.
- Remove cover using tool #C-3954 and SP3426A weights.
|
|
REMOVE OR INSTALL HORN CONTACT AND TURN SIGNAL YOKE
- Thread horn contact wire in or out carefully (observe routing during disassembly).
- Hold yoke squarely when engaging or disengaging pivot stud.
|
|
UPPER BEARING AND RELATED PARTS
- Collapsible spacer not reused (discard).
- Parts must be aligned and in sequence: upper bearing, inner race, bearing seat, retainer, rubber washer, collapsible spacer, washer, and snap ring.
|
|
UNHOOK TILT RETURN SPRINGS
- Tilt to upward position to reduce tension.
|
|
REMOVE ACTUATOR HOUSING PIVOT PINS
- Use tool #C-3957 - screw must not turn.
|
|
REMOVE OR INSTALL ACTUATOR
- Lift tilt lever so lock shoes will clear pins.
|
|
REMOVE OR INSTALL STEERING SHAFT
- Note position of lower bearing.
- Remove tilt return springs.
|
|
REMOVE OR INSTALL SPRING FROM SPHERICAL BEARING
- Tilt upper shaft approximately 10 degrees.
|
|
DISASSEMBLE OR ASSEMBLE STEERING SHAFT
- Turn upper shaft 90 degrees from centerline.
- Align flats on sphere with socket.
- Lift upper shaft and sphere from lower shaft. (Assemble in same position)
|
|
ALIGN SPLINES WHEN ASSEMBLING
- Imperial - Mark on upper shaft must be aligned with center of bolt groove (flat) on lower shaft.
- Chrysler and 880 - With mark on upper shaft at 12 o�clock, scribed mark in groove at lower end must be at 9 o�clock.
|
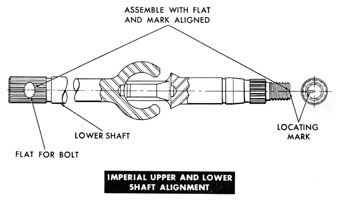
|
REMOVE OR INSTALL ACTUATOR HOUSING SUPPORT AND LOCK PLATE
- Note position of short screws.
- Lock plate slides in or out of slots.
|
|
REMOVE OR INSTALL TURN SIGNAL SWITCH CONTROL CABLE
- Remove or install attaching screw.
- Disengage bowden wire from belicrank.
- Note position of bowden wire coils.
|
|
REMOVE OR INSTALL LOCK SHOE PIVOT PINS
- Back up boss with piece of steel.
- Use 1/8" punch.
|
|
REMOVE OR INSTALL LOCK SHOES
- Carefully pry lock shoes over yoke with screw driver.
|
|
UPPER AND LOWER LOCK SHOES
- Upper lock shoe has three notches and rubber bumper. Lower lock shoe has four notches.
- Note position of tension springs.
|
|
INSTALL ACTUATOR PIVOT PINS
- 3/8" rod under yoke helps align pin holes.
- Pins must be seated.
|
|
HOOK TILT RETURN SPRINGS OVER TABS
- Tilt to full upward position.
- Use tool C-3956.
- Spring ends must hook upward as shown.
|
|
INSTALL UPPER BEARING AND RELATED PARTS
- Use new collapsible spacer.
- Use tool C-3957.
- Parts must be aligned and in sequence: upper bearing, inner race, bearing seat, retainer, rubber washer, collapsible spacer, washer, snap ring.
- Snap ring must be fully seated.
|
|
CHECK SHAFT ROTATING TORQUE
- Use inch pound torque wrench.
- Check in all tilt positions.
- If maximum reading is over 2 1/2 inch pounds, replace collapsible spacer.
|
|
INSTALL TURN SIGNAL COVER
|
|
LOWER SHAFT BEARING - IMPERIAL ONLY
- Spring, bearing and plastic support held in place by coupling with bolt.
- Carefully pry out support to avoid breakage.
|
|
|